Polysonic Wind Tunnel
The polysonic wind tunnel at the Florida State University is capable of operating in the Mach number regime of 0.2 to 5 including transonic speeds and produces a unit Reynolds number of 30 million/ft. The facility features two separate test sections:
- 12" x 12" x 24" test section with solid walls for sub/supersonic Mach number testing
- 12" x 12" x 48" with slotted walls for testing in the transonic speed regime
Typical run duration at supersonic Mach numbers is 60 seconds. The wind tunnel is equipped with required instrumentation including a six component strain gauge balance to measure aerodynamic forces and moments, an electronic pressure scanner (ESP) for steady pressure distributions and Kulite pressure transducers for unsteady pressures. The facility is designed for maximum optical access and with flow diagnostic capabilities such as Schlieren, shadowgraph and surface oil flow visualizations. The side windows in the supersonic test section are fitted with optical quality glass. Test models can be either roof/floor-mounted or supported by a sting and pitch / roll mechanism capable of pitch (α = -10° to +12°) and roll (±180°) during the blowdown. The polysonic wind tunnel is designed to produce excellent flow quality. This is achieved through 10:1 inlet contraction ratio, 5 fine mesh flow conditioning screens, flow straightener and settling chamber acoustic treatment.
Services
Measurements & Diagnostics
- Six-Component Force & Movement Measurements
- Steady and Unsteady Pressure Distribution
- Schlieren, Shadowgraph, & Surface Oil Flow Visualization
- Background Oriented Schlieren (BOS)
- Particle Image Velocimetry (PIV)
- Planar Laser Induced Fluorescence (PLIF)
- Pressure Sensitive Paint (PSP)
- Malley Probe / Shack-Hartmann System for optical distortion testing
- Sub/Supersonic Inlet Characterization
- Half Model Testing
Timeframes & Availability
Standard Testing
Force & moment measurements, Steady & unsteady pressure measurements, Flow visualization etc.
Test preparation time : 1-2 days (typ.)
Blowdowns per day: 6 - 8 (typ.)
Complex Diagnostics
Particle Image Velocimetry, Pressure Sensitive Paints, BOS etc.
Test preparation time : 2-3 days (typ.)
Blowdowns per day: 4 - 6 (typ.)
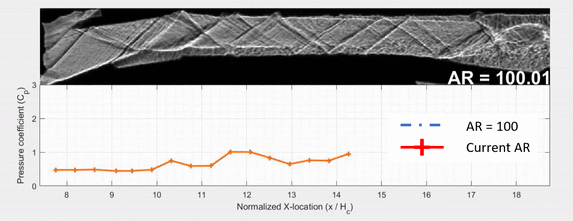